Jak zintegrować relokację z cyfryzacją zakładu? Praktyczny przewodnik Industry 4.0
Czwarta rewolucja przemysłowa stawia przed zakładami produkcyjnymi nowe wymagania, ale i otwiera przed nimi szanse na modernizację w skali dotąd niespotykanej. Cyfryzacja produkcji w ramach Industry 4.0 oznacza nie tylko automatyzację przemysłu, lecz także pełną integrację procesów — od planowania po logistykę — z wykorzystaniem systemów MES, ERP, IIoT oraz technologii predykcyjnych i danych w czasie rzeczywistym. Relokacja zakładu staje się idealnym momentem, by połączyć transformację cyfrową z reorganizacją infrastruktury.
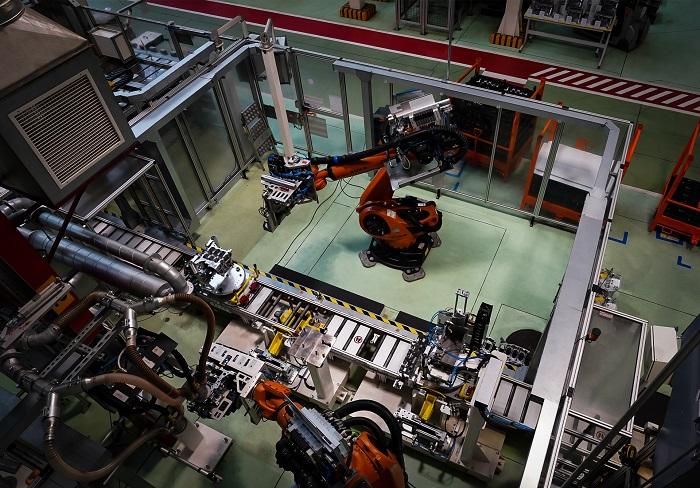
Integracja z MES i ERP w kontekście Industry 4.0 i relokacji
Systemy MES i ERP to niezbędne narzędzia nowoczesnej fabryki. ERP odpowiada za planowanie zasobów, zarządzanie zapasami i logistykę, podczas gdy MES nadzoruje procesy produkcyjne w czasie rzeczywistym. W procesie relokacji oba narzędzia umożliwiają synchronizację fizycznego przenoszenia maszyn z cyfrowym odzwierciedleniem ich działania — od wirtualnej symulacji nowego layoutu po monitorowanie wydajności zaraz po uruchomieniu produkcji.
Przygotowując harmonogram relokacji, dane z ERP i MES pozwalają na:
-
precyzyjne zaplanowanie etapów demontażu i ponownego montażu,
-
synchronizację dostaw i transportu,
-
kalkulację zasobów oraz kosztów z dokładnością do pojedynczego komponentu,
-
zminimalizowanie przestojów poprzez planowanie okien przestojowych,
-
ciągłość monitoringu parametrów pracy linii po uruchomieniu w nowej lokalizacji.
Przeanalizowanie obecnej infrastruktury i procesów
Zanim rozpocznie się demontaż urządzeń, konieczna jest inwentaryzacja maszyn oraz audyt aktualnego layoutu, przepływu materiałów, łączności IT i punktów energetycznych. Narzędziem wspierającym analizę jest cyfrowy bliźniak (Digital Twin), który pozwala zasymulować nową przestrzeń i przetestować przyszłe ustawienia maszyn, układ gniazd produkcyjnych i ścieżki logistyczne bez przerywania bieżących operacji.
Automatyzacja i monitoring w czasie rzeczywistym
W nowej lokalizacji warto wdrożyć zrobotyzowane stanowiska, coboty, AGV oraz sieć sensorów IIoT do bieżącej analizy danych produkcyjnych. Dzięki automatyzacji można zmniejszyć zależność od pracy fizycznej, przyspieszyć procesy, obniżyć koszty jednostkowe oraz ułatwić śledzenie produkcji i stanu maszyn. Takie podejście wspiera predykcyjne utrzymanie ruchu i pozwala uniknąć nieplanowanych przestojów.
Bezpieczeństwo danych i zgodność z normami
Transformacja cyfrowa wymaga zabezpieczenia komunikacji między urządzeniami i systemami IT. Wdrożenie MES/ERP powinno uwzględniać:
-
politykę backupów i ochrony danych,
-
szyfrowanie transmisji,
-
zgodność z normami ISO 27001 i BHP,
-
dokumentację powykonawczą z uwzględnieniem CE i lokalnych przepisów.
Korzyści z integracji relokacji i cyfryzacji
Integracja relokacji z cyfryzacją zakładu pozwala na pełną optymalizację procesów produkcyjnych. Dzięki cyfrowemu odwzorowaniu linii technologicznych jeszcze przed przeniesieniem możliwe jest wirtualne przetestowanie różnych układów i ścieżek logistycznych, co znacząco zwiększa efektywność nowej konfiguracji.
Wdrożenie systemów ERP i MES w trakcie relokacji pozwala znacząco zredukować przestoje. Precyzyjne harmonogramowanie prac, oparte na danych z systemów, umożliwia dokładne zaplanowanie transportu, montażu oraz ponownego uruchomienia produkcji. W wielu przypadkach czas przestoju udaje się skrócić nawet o 30%.
Zastosowanie technologii IoT i automatyzacji zapewnia bieżącą kontrolę nad produkcją. Czujniki i systemy monitorujące dostarczają danych w czasie rzeczywistym, co pozwala szybciej reagować na zakłócenia, przewidywać awarie i minimalizować straty. Lepsza kontrola nad procesami produkcyjnymi oznacza również wyższą jakość wytwarzanych produktów i niższy odsetek braków.
Dodatkowo integracja systemów cyfrowych z relokacją wzmacnia bezpieczeństwo operacyjne firmy. Cyfrowa dokumentacja, automatyczne raportowanie oraz zgodność z normami ISO i BHP ułatwiają kontrolę jakości i przygotowanie do audytów. W efekcie firma zyskuje nie tylko nowoczesne środowisko pracy, ale również większą przewidywalność operacyjną i lepsze zarządzanie ryzykiem.
Relokacja fabryki przestaje być wyłącznie operacją logistyczną. W epoce Industry 4.0 staje się punktem wyjścia do strategicznej transformacji technologicznej. Integracja z systemami ERP, MES i IIoT nie tylko usprawnia proces przeniesienia, lecz także pozwala zaprojektować produkcję na nowo – inteligentną, elastyczną i gotową na wyzwania rynku. Aby osiągnąć sukces, warto współpracować z partnerami doświadczonymi zarówno w relokacji, jak i w cyfryzacji. Jednym z takich dostawców kompleksowych rozwiązań jest ESOX Industrial Automation z Łodygowic.
Dodaj komentarz